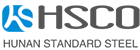
Differences between API 5L PSL1 and PSL2:
API 5L Standard has the provisions of the two product specification levels (PSL1 and PSL2). The two kinds of PSL grade level of the product to the standard stipulated in the technical requirements of different, PSL2 of carbon equivalent, notch toughness, maximum yield strength and tensile strength have mandatory requirements.
PSL is short for product specification level. API 5L Line pipe product specification level is divided into PSL1 and PSL2, also can say quality grades are divided into PSL1 and PSL2. PSL2 above PSL1, these two levels is not only different inspection requirements, and chemical composition, mechanical performance requirements are different, so the order in API 5 l, the terms of the contract in addition to indicate the specifications and grade of steel usually indicators, must also indicate the level of product specification, namely PSL1 or PSL2.
PSL2 in chemical composition, tensile properties, impact energy, and nondestructive testing which strict in PSL1 indicators. PSL1 does not require impact performance, PSL2 all except x80 grade steel, full size 0 ℃ average Akv: longitudinal p j, 41 lateral acuity 27 j.Average grade X80 steel, full size 0 ℃ Akv: longitudinal 101 j, or lateral acuity 68 j. Line pipe should do water pressure test, and the standards are not allowed to nondestructive generation of hydraulic pressure, which is also the API standard and one big difference between our country standard.PSL1 does not require the nondestructive inspection, PSL2 shall by a nondestructive examination.
Manufacturing process:
Seamless pipe: produced by hot rolling or cold drawing process, suitable for high pressure and small diameter pipes, but the cost is higher.
Welded pipe: including high frequency electric resistance welding (ERW) and submerged arc welding (SAW), which dominates the field of large diameter (such as ≥24 inches) and has lower cost.
API 5L Standard Mechanical properties:
Standard
Steel Grade
Yield Strength(MPa)
Tensile Strength(MPa)
API 5L
PSL1
A25
172
310
A
207
331
B
241
414
X42
290
414
X46
317
434
X52
359
455
X56
386
490
X60
414
517
X65
448
531
X70
483
565
PSL2
241-448
414-758
B
290-496
414-758
X42
317-524
434-758
X46
359-531
455-758
X52
386-544
490-758
X56
414-565
517-758
X60
448-600
531-758
X65
483-621
565-758
X70
552-690
621-827
Delivery condition:
PSL | Delivery Condition | Pipe grade |
---|---|---|
PSL1 | As-rolled, normalized, normalizing formed | A |
As-rolled, normalizing rolled, thermomechanical rolled, thermo-mechanical formed, normalizing formed, normalized, normalized and tempered or if agreed Q&T SMLS only | B | |
As-rolled, normalizing rolled, thermomechanical rolled, thermo-mechanical formed, normalizing formed, normalized, normalized and tempered | X42, X46, X52, X56, X60, X65, X70 | |
PSL 2 | As-rolled | BR, X42R |
Normalizing rolled, normalizing formed, normalized or normalized and tempered | BN, X42N, X46N, X52N, X56N, X60N | |
Quenched and tempered | BQ, X42Q, X46Q, X56Q, X60Q, X65Q, X70Q, X80Q, X90Q, X100Q | |
Thermomechanical rolled or thermomechanical formed | BM, X42M, X46M, X56M, X60M, X65M, X70M, X80M | |
Thermomechanical rolled | X90M, X100M, X120M | |
The suffice (R, N, Q or M) for PSL2 grades, belongs to the steel grade |
Chemical requirements:
Chemical Composition for PSL 1 pipe with t ≤ 0.984”
Steel Grade | Mass fraction, % based on heat and product analyses a,g | ||||||
---|---|---|---|---|---|---|---|
C | Mn | P | S | V | Nb | Ti | |
max b | max b | max | max | max | max | max | |
Seamless Pipe | |||||||
A | 0.22 | 0.9 | 0.3 | 0.3 | – | – | – |
B | 0.28 | 1.2 | 0.3 | 0.3 | c,d | c,d | d |
X42 | 0.28 | 1.3 | 0.3 | 0.3 | d | d | d |
X46 | 0.28 | 1.4 | 0.3 | 0.3 | d | d | d |
X52 | 0.28 | 1.4 | 0.3 | 0.3 | d | d | d |
X56 | 0.28 | 1.4 | 0.3 | 0.3 | d | d | d |
X60 | 0.28 e | 1.40 e | 0.3 | 0.3 | f | f | f |
X65 | 0.28 e | 1.40 e | 0.3 | 0.3 | f | f | f |
X70 | 0.28 e | 1.40 e | 0.3 | 0.3 | f | f | f |
Welded Pipe | |||||||
A | 0.22 | 0.9 | 0.3 | 0.3 | – | – | – |
B | 0.26 | 1.2 | 0.3 | 0.3 | c,d | c,d | d |
X42 | 0.26 | 1.3 | 0.3 | 0.3 | d | d | d |
X46 | 0.26 | 1.4 | 0.3 | 0.3 | d | d | d |
X52 | 0.26 | 1.4 | 0.3 | 0.3 | d | d | d |
X56 | 0.26 | 1.4 | 0.3 | 0.3 | d | d | d |
X60 | 0.26 e | 1.40 e | 0.3 | 0.3 | f | f | f |
X65 | 0.26 e | 1.45 e | 0.3 | 0.3 | f | f | f |
X70 | 0.26e | 1.65 e | 0.3 | 0.3 | f | f | f |
a. Cu ≤ = 0.50% Ni; ≤ 0.50%; Cr ≤ 0.50%; and Mo ≤ 0.15%, b. For each reduction of 0.01% below the specified maximum concentration for carbon, an increase of 0.05% above the specified maximum concentration for Mn is permissible, up to a maximum of 1.65% for grades ≥ L245 or B, but ≤ L360 or X52; up to a maximum of 1.75% for grades > L360 or X52, but < L485 or X70; and up to a maximum of 2.00% for grade L485 or X70., c. Unless otherwise agreed NB + V ≤ 0.06%, d. Nb + V + TI ≤ 0.15%, e. Unless otherwise agreed., f. Unless otherwise agreed, NB + V = Ti ≤ 0.15%, g. No deliberate addition of B is permitted and the residual B ≤ 0.001% |
Chemical Composition for PSL 2 pipe with t ≤ 0.984”
Steel Grade | Mass fraction, % based on heat and product analyses | Carbon Equiv a | |||||||||||||||||||
---|---|---|---|---|---|---|---|---|---|---|---|---|---|---|---|---|---|---|---|---|---|
C | Si | Mn | P | S | V | Nb | Ti | Other | CE IIW | CE Pcm | |||||||||||
max b | max | max b | max | max | max | max | max | max | max | ||||||||||||
Seamless and Welded Pipe | |||||||||||||||||||||
BR | 0.24 | 0.4 | 1.2 | 0.025 | 0.015 | c | c | 0.04 | e,l | 0.43 | 0.25 | ||||||||||
X42R | 0.24 | 0.4 | 1.2 | 0.025 | 0.015 | 0.06 | 0.05 | 0.04 | e,l | 0.43 | 0.25 | ||||||||||
BN | 0.24 | 0.4 | 1.2 | 0.025 | 0.015 | c | c | 0.04 | e,l | 0.43 | 0.25 | ||||||||||
X42N | 0.24 | 0.4 | 1.2 | 0.025 | 0.015 | 0.06 | 0.05 | 0.04 | e,l | 0.43 | 0.25 | ||||||||||
X46N | 0.24 | 0.4 | 1.4 | 0.025 | 0.015 | 0.07 | 0.05 | 0.04 | d,e,l | 0.43 | 0.25 | ||||||||||
X52N | 0.24 | 0.45 | 1.4 | 0.025 | 0.015 | 0.1 | 0.05 | 0.04 | d,e,l | 0.43 | 0.25 | ||||||||||
X56N | 0.24 | 0.45 | 1.4 | 0.025 | 0.015 | 0.10f | 0.05 | 0.04 | d,e,l | 0.43 | 0.25 | ||||||||||
X60N | 0.24f | 0.45f | 1.40f | 0.025 | 0.015 | 0.10f | 0.05f | 0.04f | g,h,l | As agreed | |||||||||||
BQ | 0.18 | 0.45 | 1.4 | 0.025 | 0.015 | 0.05 | 0.05 | 0.04 | e,l | 0.43 | 0.25 | ||||||||||
X42Q | 0.18 | 0.45 | 1.4 | 0.025 | 0.015 | 0.05 | 0.05 | 0.04 | e,l | 0.43 | 0.25 | ||||||||||
X46Q | 0.18 | 0.45 | 1.4 | 0.025 | 0.015 | 0.05 | 0.05 | 0.04 | e,l | 0.43 | 0.25 | ||||||||||
X52Q | 0.18 | 0.45 | 1.5 | 0.025 | 0.015 | 0.05 | 0.05 | 0.04 | e,l | 0.43 | 0.25 | ||||||||||
X56Q | 0.18 | 0.45f | 1.5 | 0.025 | 0.015 | 0.07 | 0.05 | 0.04 | e,l | 0.43 | 0.25 | ||||||||||
X60Q | 0.18f | 0.45f | 1.70f | 0.025 | 0.015 | g | g | g | h,l | 0.43 | 0.25 | ||||||||||
X65Q | 0.18f | 0.45f | 1.70f | 0.025 | 0.015 | g | g | g | h,l | 0.43 | 0.25 | ||||||||||
X70Q | 0.18f | 0.45f | 1.80f | 0.025 | 0.015 | g | g | g | h,l | 0.43 | 0.25 | ||||||||||
X80Q | 0.18f | 0.45f | 1.90f | 0.025 | 0.015 | g | g | g | i,j | As agreed | |||||||||||
X90Q | 0.16f | 0.45f | 1.9 | 0.02 | 0.01 | g | g | g | j,k | As agreed | |||||||||||
X100Q | 0.16f | 0.45f | 1.9 | 0.02 | 0.01 | g | g | g | j,k | As agreed | |||||||||||
Welded Pipe | |||||||||||||||||||||
BM | 0.22 | 0.45 | 1.2 | 0.025 | 0.015 | 0.05 | 0.05 | 0.04 | e,l | 0.43 | 0.25 | ||||||||||
X42M | 0.22 | 0.45 | 1.3 | 0.025 | 0.015 | 0.05 | 0.05 | 0.04 | e,l | 0.43 | 0.25 | ||||||||||
X46M | 0.22 | 0.45 | 1.3 | 0.025 | 0.015 | 0.05 | 0.05 | 0.04 | e,l | 0.43 | 0.25 | ||||||||||
X52M | 0.22 | 0.45 | 1.4 | 0.025 | 0.015 | d | d | d | e,l | 0.43 | 0.25 | ||||||||||
X56M | 0.22 | 0.45f | 1.4 | 0.025 | 0.015 | d | d | d | e,l | 0.43 | 0.25 | ||||||||||
X60M | 0.12f | 0.45f | 1.60f | 0.025 | 0.015 | g | g | g | h,l | 0.43 | 0.25 | ||||||||||
X65M | 0.12f | 0.45f | 1.60f | 0.025 | 0.015 | g | g | g | h,l | 0.43 | 0.25 | ||||||||||
X70M | 0.12f | 0.45f | 1.70f | 0.025 | 0.015 | g | g | g | h,l | 0.43 | 0.25 | ||||||||||
X80M | 0.12f | 0.45f | 1.85f | 0.025 | 0.015 | g | g | g | i,j | .043f | 0.25 | ||||||||||
X90M | 0.1 | 0.55f | 2.10f | 0.02 | 0.01 | g | g | g | i,j | – | 0.25 | ||||||||||
X100M | 0.1 | 0.55f | 2.10f | 0.02 | 0.01 | g | g | g | i,j | – | 0.25 | ||||||||||
a. SMLS t>0.787”, CE limits shall be as agreed. The CEIIW limits applied fi C > 0.12% and the CEPcm limits apply if C ≤ 0.12%, b. For each reduction of 0.01% below the specified maximum for C, an increase of 0.05% above the specified maximum for Mn is permissible, up to a maximum of 1.65% for grades ≥ L245 or B, but ≤ L360 or X52; up to a maximum of 1.75% for grades > L360 or X52, but < L485 or X70; up to a maximum of 2.00% for grades ≥ L485 or X70, but ≤ L555 or X80; and up to a maximum of 2.20% for grades > L555 or X80., c. Unless otherwise agreed Nb = V ≤ 0.06%, d. Nb = V = Ti ≤ 0.15%, e. Unless otherwise agreed, Cu ≤ 0.50%; Ni ≤ 0.30% Cr ≤ 0.30% and Mo ≤ 0.15%, f. Unless otherwise agreed, g. Unless otherwise agreed, Nb + V + Ti ≤ 0.15%, h. Unless otherwise agreed, Cu ≤ 0.50% Ni ≤ 0.50% Cr ≤ 0.50% and MO ≤ 0.50%, i. Unless otherwise agreed, Cu ≤ 0.50% Ni ≤ 1.00% Cr ≤ 0.50% and MO ≤ 0.50%, j. B ≤ 0.004%, k. Unless otherwise agreed, Cu ≤ 0.50% Ni ≤ 1.00% Cr ≤ 0.55% and MO ≤ 0.80%, l. For all PSL 2 pipe grades except those grades with footnotes j noted, the following applies. Unless otherwise agreed no intentional addition of B is permitted and residual B ≤ 0.001%. |
Pipe Grade | Tensile Properties – Pipe Body of SMLS and Welded Pipes PSL 1 | Seam of Welded Pipe | ||
---|---|---|---|---|
Yield Strength a | Tensile Strength a | Elongation | Tensile Strength b | |
Rt0,5 PSI Min | Rm PSI Min | (in 2in Af % min) | Rm PSI Min | |
A | 30,500 | 48,600 | c | 48,600 |
B | 35,500 | 60,200 | c | 60,200 |
X42 | 42,100 | 60,200 | c | 60,200 |
X46 | 46,400 | 63,100 | c | 63,100 |
X52 | 52,200 | 66,700 | c | 66,700 |
X56 | 56,600 | 71,100 | c | 71,100 |
X60 | 60,200 | 75,400 | c | 75,400 |
X65 | 65,300 | 77,500 | c | 77,500 |
X70 | 70,300 | 82,700 | c | 82,700 |
a. For intermediate grade, the difference between the specified minimum tensile strength and the specified minimum yield for the pipe body shall be as given for the next higher grade. | ||||
b. For the intermediate grades, the specified minimum tensile strength for the weld seam shall be the same as determined for the body using foot note a. | ||||
c. The specified minimum elongation, Af, expressed in percent and rounded to the nearest percent, shall be determined using the following equation: | ||||
![]() |
||||
Where C is 1 940 for calculation using Si units and 625 000 for calculation using USC units | ||||
Axc is the applicable tensile test piece cross-sectional area, expressed in square millimeters (square inches) , as follows | ||||
– For circular cross-section test pieces, 130mm2 (0.20 in2) for 12.7 mm (0.500 in) and 8.9 mm (.350 in) diameter test pieces; and 65 mm2 (0.10 in2) for 6.4 mm (0.250in) diameter test pieces. | ||||
– For full-section test pieces, the lesser of a) 485 mm2 (0.75 in2) and b) the cross-sectional area of the test piece, derived using the specified outside diameter and the specified wall thickness of the pipe, rounded to the nearest 10 mm2 (0.10in2) | ||||
– For strip test pieces, the lesser of a) 485 mm2 (0.75 in2) and b) the cross-sectional area of the test piece, derived using the specified width of the test piece and the specified wall thickness of the pipe, rounded to the nearest 10 mm2 (0.10in2) | ||||
U is the specified minimum tensile strength, expressed in megapascals (pounds per square inch)
|
Pipe Grade | Tensile Properties – Pipe Body of SMLS and Welded Pipes PSL 2 | Seam of Welded Pipe | |||||
---|---|---|---|---|---|---|---|
Yield Strength a | Tensile Strength a | Ratio a,c | Elongation | Tensile Strength d | |||
Rt0,5 PSI Min | Rm PSI Min | R10,5IRm | (in 2in) | Rm (psi) | |||
Af % | |||||||
Minimum | Maximum | Minimum | Maximum | Maximum | Minimum | Minimum | |
BR, BN,BQ,BM | 35,500 | 65,300 | 60,200 | 95,000 | 0.93 | f | 60,200 |
X42,X42R,X2Q,X42M | 42,100 | 71,800 | 60,200 | 95,000 | 0.93 | f | 60,200 |
X46N,X46Q,X46M | 46,400 | 76,100 | 63,100 | 95,000 | 0.93 | f | 63,100 |
X52N,X52Q,X52M | 52,200 | 76,900 | 66,700 | 110,200 | 0.93 | f | 66,700 |
X56N,X56Q,X56M | 56,600 | 79,000 | 71,100 | 110,200 | 0.93 | f | 71,100 |
X60N,X60Q,S60M | 60,200 | 81,900 | 75,400 | 110,200 | 0.93 | f | 75,400 |
X65Q,X65M | 65,300 | 87,000 | 77,600 | 110,200 | 0.93 | f | 76,600 |
X70Q,X65M | 70,300 | 92,100 | 82,700 | 110,200 | 0.93 | f | 82,700 |
X80Q,X80M | 80,.500 | 102,300 | 90,600 | 119,700 | 0.93 | f | 90,600 |
a. For intermediate grade, refer to the full API5L specification. | |||||||
b. for grades > X90 refer to the full API5L specification. | |||||||
c. This limit applies for pies with D> 12.750 in | |||||||
d. For intermediate grades, the specified minimum tensile strength for the weld seam shall be the same value as was determined for the pipe body using foot a. | |||||||
e. for pipe requiring longitudinal testing, the maximum yield strength shall be ≤ 71,800 psi | |||||||
f. The specified minimum elongation, Af, expressed in percent and rounded to the nearest percent, shall be determined using the following equation: | |||||||
![]() |
|||||||
Where C is 1 940 for calculation using Si units and 625 000 for calculation using USC units | |||||||
Axc is the applicable tensile test piece cross-sectional area, expressed in square millimeters (square inches) , as follows | |||||||
– For circular cross-section test pieces, 130mm2 (0.20 in2) for 12.7 mm (0.500 in) and 8.9 mm (.350 in) diameter test pieces; and 65 mm2 (0.10 in2) for 6.4 mm (0.250in) diameter test pieces. | |||||||
– For full-section test pieces, the lesser of a) 485 mm2 (0.75 in2) and b) the cross-sectional area of the test piece, derived using the specified outside diameter and the specified wall thickness of the pipe, rounded to the nearest 10 mm2 (0.10in2) | |||||||
– For strip test pieces, the lesser of a) 485 mm2 (0.75 in2) and b) the cross-sectional area of the test piece, derived using the specified width of the test piece and the specified wall thickness of the pipe, rounded to the nearest 10 mm2 (0.10in2) | |||||||
U is the specified minimum tensile strength, expressed in megapascals (pounds per square inch | |||||||
g. Lower values fo R10,5IRm may be specified by agreement | |||||||
h. for grades > x90 refer to the full API5L specification. |
API 5L Pipe Quality Inspection Standards:
Hydrostatic Test
The pipe shall be subjected to a hydrostatic test with no leakage in the weld or pipe body. If the pipe section used has successfully passed the test, the joint does not need to be hydrostatically tested.
Bend Test
No cracks shall be present in any part of the test piece and no openings shall be present in the weld.
Flattening Test
The acceptance criteria for the flattening test shall be:
EW Pipe D<12.750 inches:
X60, T 500 inches. The weld shall not open until the distance between the plates is less than 66% of the original outside diameter. For all grades and wall thicknesses, it is 50%.
For pipes with D/t > 10, the weld shall not open until the distance between the plates is less than 30% of the original outside diameter.
For other sizes, refer to the complete API 5L specification.
CVN Impact Test for PSL2
Many PSL2 pipe sizes and grades require CVN. Seamless pipe will be tested inside the pipe body. Welded pipe is tested on the pipe body, pipe welds, and heat affected zone. Refer to the full API 5L specification for sizes and grades and a chart of required absorbed energy values.
Read more: American Standard Seamless Steel Pipe or API 5L ERW Standard line Pipe
Related information