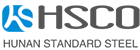
What is a 45 degree pipe elbow?
45 degree elbow (45°) is a pipe fitting and pipe connector. Elbows are used in main pipes and branch pipes to change the direction of the pipe. They are an indispensable part of the pipeline system. Pipe elbows are divided into angles, with 45°, 90° and 180° being the most commonly used. The main ways to connect elbows and pipes include: direct welding (the most commonly used method), flange connection, hot-melt connection, electrofusion connection, threaded connection and socket connection, etc.
Divided according to material: carbon steel, cast steel, alloy steel, stainless steel, non-ferrous metals, plastics, etc.
In the pipeline system, due to the influence of thermal expansion, contraction, vibration and other factors, the pipeline generates stress. Sudden direction changes will cause stress concentration and increase the fatigue load of the pipeline and connecting parts. 45-degree elbows disperse stress and reduce fatigue damage to piping systems by providing smoother changes in direction. This is especially important for pipeline systems with high pressure, high temperature and high flow rate, helping to extend the service life of the pipeline and reduce maintenance costs.
How to make 45 degree pipe elbow?
Elbow making method 1: pushing
Push elbow is the most important forming production process of elbow. A pushing machine, mandrel mold and heating equipment are required. The finished tube blank is placed on the mandrel and is pushed, heated and formed at the same time. This method has fast production speed and is suitable for mass production. The elbow produced has beautiful appearance and relatively uniform thickness. It has become the main forming method for carbon steel elbows and alloy steel elbows, and is also used for some specifications of stainless steel elbows.
Elbow making method 2: stamping
Stamping is an early elbow forming manufacturing process. Depending on the material, you can choose cold pressing or hot pressing. Put the tube blank into the outer mold. After the upper and lower molds are merged, under the push of the press, the tube blank moves along the gap reserved between the inner mold and the outer mold to complete the forming process. Stamping has been replaced by pushing or other production methods. For certain specifications of elbows, due to the small production volume and the wall thickness is too thick or too thin, the stamping process can be selected.
Elbow making method 3: butt welding
The butt welding elbow is made of steel plate. Draw a picture to draw the unfolded diagram of the butt welding elbow. Then cut the material with gas, then heat and press it on the press. Then two and a half pieces of elbow come out, and then the cutting is done. Then splicing and welding, the butt welding elbow is formed. Butt welding elbows are mainly used for large-scale elbow production. Large-diameter elbows can also be pushed and stamped. However, the process cost of butt welding elbows is lower than either of the two.
Elbow making method 4: shrimp waist
Shrimp waist elbow is welded by using multiple sections of coiled pipe with different angles. Compared with the first three processes, shrimp waist elbow has much fewer applications. This process is suitable for manufacturing large elbows of any size with elbows larger than 1.5D.
45 degree elbow fittings play an important role in piping systems, optimizing the performance and life of the piping system by changing the direction of the pipe, connecting different pipe sections, and reducing pipe stress. 45-degree elbows are widely used in petroleum, natural gas, chemical industry, electric power and other fields and are an indispensable key component in pipeline engineering. Choosing appropriate materials, ensuring installation quality, and performing regular maintenance are the keys to ensuring safe and reliable operation of the pipeline system.
Read more: Types, advantages and disadvantages of elbow fittings
Related information