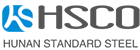
SSAW pipe is made of hot rolled coiled steel by automatic submerged arc weld under normal atmospheric temperature. There are 12 sets of modernized production line of SSAW pipe. The annual yield of SSAW pipe with outside diameter 219mm-
3620mm,wall thickness 5-25.4mm and steel grade B-X80. Its two steel pipe production lines, one for spiral submerged arc welded steel pipe and one for longitudinal submerged arc welded steel pipe, are respectively comprised of two sets of main machines and 1 set of sizing equipment.
1. Coil Probe: steel coil into the production line, the first full board Ultrasonic Inspection
2. Leveling Milling: through anvil plate leveling machine so that the original curl, and then pass the two edges of steel-sided milling machine milling, so that up to the requirements of the plate width, plate edge parallel groove shape
3. Cut Type: steel production line along the outer edge of the coiled-coil tube
4. welding and cutting: the use of advanced technology for pre double submerged arc welding(dsaw) cutting inside from the foot of the welding specification welded steel pipe welded outside use, etc.
5. Visual inspection: some basic parameters by a professional technician check
6. ultrasonic flaw: the inner and outer sides of the base metal and weld seam 100% inspection
7. X-ray detection: internal and external welds 100% X-ray television industry checks, the use of image processing system ensures detection sensitivity
8. Pressure test: hydrostatic testing machine by-root test steel pipe up to the standard requirements to ensure that the test pressure
9. Chamfer level: steel pipe inspection pipe end processing, up to the requirements of the pipe end beveling size
10. Check: X-rays and then subjected to ultrasonic testing and magnetic particle inspection conducted pipe end, check whether the deposit welding problems and defects in the pipe ends.
11. Oiled Marking: Qualified oiled steel pipe corrosion and in accordance with user requirements for marking.