Installation precautions for welded steel pipes
Keywords: welded steel pipe installation precautions, welded pipe welding, pipeline welding
Welded steel pipes refer to steel pipes with seams on the surface that are formed by bending steel strips or steel plates into round, square and other shapes and then welding them. The blanks used for welded steel pipes are steel plates or strip steel.
In recent years, with the rapid development of high-quality strip steel continuous rolling production and the advancement of welding and inspection technology, the quality of welds has been continuously improved, the variety and specifications of welded steel pipes have increased, and they have replaced seamless steel pipes in more and more fields. Welded steel pipes have lower costs and higher production efficiency than seamless steel pipes. So, what issues should be paid attention to during the installation of welded pipes?
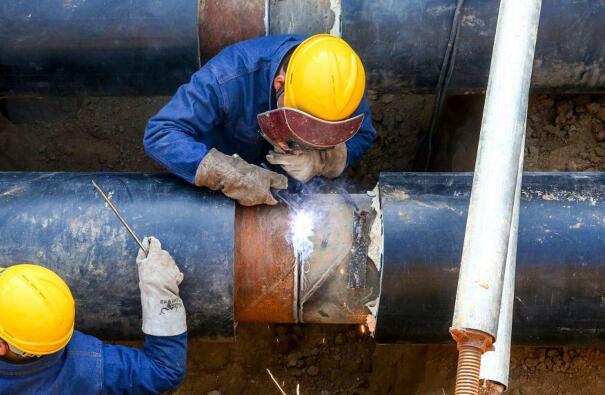
1. Pipeline cleaning
When installing welded steel pipes, first clean the pipelines, remove surface oil, rust, impurities, etc., ensure the quality of welding and connection, and prevent impurities from entering the pipeline to affect the conveying medium.
2. Material inspection
Pipeline connections must be standardized. When welding connections, check whether the pipeline material, specifications, and wall thickness meet the design requirements.
3. Welding process selection
Develop WPS (welding process specification) according to the material (carbon steel, stainless steel, alloy steel, etc.), such as Q235B commonly uses E4315 welding rods, 304 stainless steel uses A102 welding rods. Ensure that the pipeline material is compatible with the welding material to prevent cracks caused by material mismatch. The selection of welding materials should be based on the material of the parent material, such as ER70S-2 welding wire or E7018 welding rod for carbon steel. Select appropriate welding process and parameters to ensure that the weld is firm and well sealed.
3. Bevel processing
The bevel angle should be precise and the surface should be free of impurities. The outer wall of the pipe end needs to be processed with a slight chamfer (about 15°~30°) to facilitate insertion into the socket and ensure welding fusion. The bevel surface is required to be neat and smooth, and unqualified pipe ends shall not be butt welded.
4. The thread processing accuracy of the threaded connection must be ensured, and the sealing material should be wrapped to prevent leakage.
5. During the installation process, pay attention to the slope of the pipeline, such as water supply and drainage pipelines. Reasonable slope is conducive to drainage and exhaust, and avoids water accumulation and gas accumulation affecting use.
6. For parts that pass through floors, walls, etc., sleeves should be installed with appropriate sleeve diameters and waterproof and fireproof sealing.
7. When installing large-diameter or long-distance pipelines, fixed brackets and sliding brackets should be set. Fixed brackets limit pipeline displacement, and sliding brackets allow pipelines to expand and contract in a certain direction to prevent thermal expansion and contraction from causing stress and damaging pipelines.
8. Environmental protection
Carbon steel welding environment temperature is lower than -5℃ and needs to be preheated (100~150℃).
A windproof shed needs to be built when the wind speed exceeds 8m/s, and welding is prohibited when the humidity exceeds 90%. Rain, snow, strong wind and other adverse weather should be avoided during welding.
9. Post-weld treatment
For example, stress relief heat treatment needs to be kept at 600±20℃ and then slowly cooled. The weld surface should be polished to the specified height, and the welding slag and spatter should be removed to prevent corrosion.
10. Quality inspection
Non-destructive testing:
RT inspection must be qualified at level II or above, and UT inspection must meet level I standards. Strictly follow the non-destructive testing standards to ensure the quality of the weld.
Industrial pipeline spot check ratio: GC1 level 100%, GC2 level 20%
Pressure test:
The hydraulic test pressure is 1.5 times the design pressure (not less than 0.6MPa).
The air pressure test pressure is 1.15 times the design pressure, and the pressure needs to be increased step by step (10% per level).
Special working conditions:
1. Low temperature pipeline
Charpy impact test (such as ASTM A333 Gr.6) is required for working conditions below -29℃.
2. Corrosive environment
The hardness of the acidic medium pipeline after welding is ≤22HRC (NACE MR0175 standard).
It is recommended to conduct welding procedure qualification (PQR) before construction, and keep complete traceability documents such as welding material drying records (such as J427 welding rod 350℃×1h), layer temperature measurement records, etc. For special materials such as API 5L pipeline steel, attention should also be paid to the CTOD fracture toughness test requirements.
Read more: Carbon steel pipe material and classification or ERW welded pipe vs Seamless pipe cost