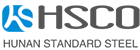
API 5CT oil casing pipe plays a vital role in the oil industry and is a pipeline used to transport resources such as oil and natural gas. In the process of manufacturing these casings, the choice of materials is crucial to their quality and performance. This article will study the application of carbon steel, stainless steel, and alloy steel in the production of oil casing, and explore their respective advantages and limitations.
Carbon steel is one of the commonly used oil casing materials. Carbon steel has become a popular choice for oil casing due to its strong strength, corrosion resistance, and cost-effectiveness. During the oil extraction process, it can withstand the high temperature and high pressure common in the extraction environment, and has excellent plasticity and weldability, and carbon steel casing is easy to manufacture and install. In addition, carbon steel can also provide high strength and rigidity to cope with complex underground environments. However, the susceptibility of carbon steel to corrosion is an obvious disadvantage, and anti-corrosion treatment is required to improve its durability.
The selection of oil casing materials should be tailored to the specific requirements of the underground operating environment. Carbon steel is usually sufficient for general downhole operations, while stainless steel is the first choice in highly corrosive environments. Alloy steel can be used in extreme temperature, high pressure, and corrosive environments. Making smart material choices can significantly improve the efficiency and safety of oil drilling operations.
Hunan Standard Steel Co., Ltd (HSCO) provides OCTG casing, tubing, and couplings of various specifications and materials. If you need any, please contact us: info@hu-steel.com
Read more: OCTG Casing Pipe Size Chart or Seamless Casing vs. ERW Casing
Related information