The defects that are often said of seamless pipes (SMLS) are the macroeconomic defects of seamless steel pipes, which can generally be seen with human eyes or a high-power magnifying glass. The defects of seamless steel pipes can be divided into surface defects and internal defects.
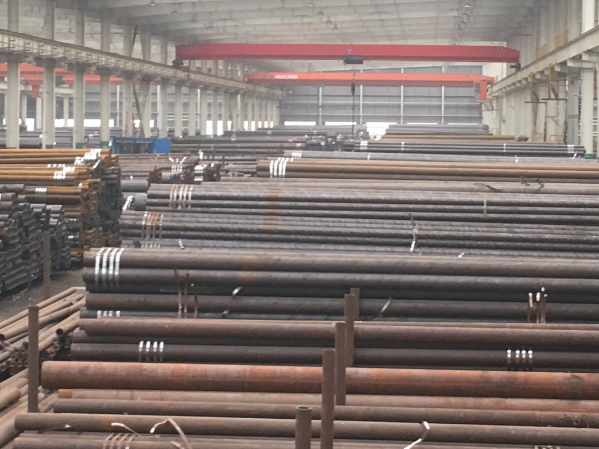
Surface defects of seamless pipes:
There are many types of surface defects in seamless pipes, such as cracks, cracks, gaps, heavy skin, surface inclusions, black spots, stretching, convex hulls, embossing, scratches, roller printing, netting, waves, drifting, There are different kinds of defects such as long knife bay, uneven thickness and burrs. Some of these defects are caused by inclusions and bubbles in the steel castings, and some may be due to poor handicrafts, but most of them are Most of them are caused by poor production line equipment, so the function of production line equipment is very important in the process of production. With the improvement of steel smelting technology and the improvement of production line equipment, theoretically speaking, the surface defects of seamless steel pipes should be lower and lower, but it should not be neglected. Only by ensuring product quality can we ensure safety and win long-term customers. Severe flaws will form the origin of fatigue failure and ductile failure. In the bolted joints of steel bridges, the compressive strength of high-strength bolted connections will continue to be reduced. Surface defects of seamless steel pipes are allowed to be eliminated by grinding wheel or hand chisel, but cannot be repaired by welding.
Internal defects of seamless pipes:
The internal defects of steel that seamless pipes often refer to generally include neck residue, air bubbles, inclusions, and shrinkage porosity. Since the seamless pipe is made of steel castings by rolling, these defects are reflected in the inside of the steel plate, forming a hierarchical structure, in which there are very few blocks, and most of them are small or partial. There are many ways to inspect these defects, and the common ones are fracture surface inspection, acid boiling or high-magnification inspection.