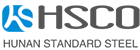
The size of oil well casing pipes, specified by their outer diameter (OD) and wall thickness, is a fundamental consideration in well construction. Properly sized casing pipes are essential for maintaining the integrity of the wellbore, preventing formation collapse, and facilitating efficient well operation. The significance of oil well casing pipe sizes can be understood through their impact on load-bearing capacity, pressure containment, and resistance to environmental stresses.
The outer diameter and wall thickness of well casing pipes directly influence their load-bearing capacity. Larger casing sizes with thicker walls are capable of withstanding higher external pressures and supporting heavier vertical loads, making them suitable for deeper wells and challenging geological formations.
Casing pipe sizes are chosen to ensure the safe containment of fluids under varying pressure conditions. Proper sizing of casing pipes is crucial in preventing well blowouts, fluid leakage, and the migration of contaminants into the surrounding environment.
Oil well casing pipe sizes are selected to withstand environmental stresses such as corrosion, abrasion, and external forces. The choice of appropriate sizes ensures the long-term durability and reliability of the well system under diverse operating conditions.
Factors influencing selection of oil well casing pipe sizes:
(1) Well Depth and Formation Characteristics
Deeper wells and unstable geological formations necessitate larger casing pipe sizes to provide adequate support and prevent collapse. Varying formation characteristics require careful assessment to determine the most suitable casing sizes for optimal well performance.
(2) Fluid Properties and Pressure Ratings
The type of fluid to be contained or extracted from the well, along with the anticipated pressure differentials, influences the selection of casing pipe sizes. Higher pressure environments or corrosive fluids may require thicker-walled casing pipes to ensure effective containment.
(3) Regulatory Compliance
Regulatory standards and industry best practices mandate minimum casing size requirements based on the intended use of the well, environmental considerations, and public safety standards. Compliance with these regulations is imperative and influences the choice of casing pipe sizes for a particular well project.
(4) Operational Considerations
The planned well completion and production techniques also influence the selection of casing pipe sizes. For instance, the installation of production tubing inside the casing may dictate larger casing sizes to allow for proper annular flow and production optimization.
Example 1: Oil and Gas Industry
In an offshore drilling project targeting a deep-sea reservoir, the selection of oil well casing pipe sizes is paramount. Given the extreme depths and high-pressure conditions encountered in offshore drilling, larger casing pipe sizes, such as 13 3/8 inches OD with heavy wall thickness, are often employed to ensure structural integrity and pressure containment. The example illustrates how casing pipe sizes are tailored to accommodate the challenging subsurface conditions prent in offshore oil and gas exploration.
Example 2: Water Well Construction
In the context of constructing a municipal water supply well, the utilization of steel casing pipe sizes is driven by the need to secure a clean and reliable water source. For a moderately deep water well serving a local community, smaller casing pipe sizes, such as 6 inches OD with standard wall thickness, may be sufficient to protect the wellbore and maintain water quality. This example demonstrates how casing pipe sizes are adapted to meet the specific depth and aquifer characteristics typical of water well construction projects.
Example 3: Geothermal Energy Extraction
In a geothermal energy extraction project targeting a high-temperature reservoir, the selection of steel well casing pipe sizes is influenced by the extreme downhole conditions. Large-diameter casing pipes, such as 9 5/8 inches OD with enhanced wall thickness to withstand thermal stresses, are employed to facilitate the installation of downhole heat exchangers and ensure the integrity of the geothermal well. This example highlights the customization of casing pipe sizes to address the unique challenges associated with geothermal energy extraction.
Conclusion:
Oil well casing pipe sizes are pivotal in ensuring the success and sustainability of well construction across diverse industries. By carefully uating factors such as well depth, formation characteristics, regulatory compliance, and operational considerations, engineers and operators can select the most suitable casing pipe sizes to meet the specific requirements of each well project. The clear examples provided underscore the adaptable nature of oil well casing pipe sizes, demonstrating their critical role in addressing the varied challenges posed by different well construction scenarios. Through informed decision-making and precise sizing, the industry can continue to enhance the safety, efficiency, and longevity of well systems.
Read more: What are the steel grades of OCTG casing?
Related information