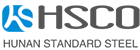
The thick-walled elbow structure is reasonable, the pipe system can be evenly stressed, the pipe system can be simplified, the operation is convenient, the investment can be saved, the pipe resistance can be reduced, the pipe arrangement can be optimized, the operation cost can be reduced, the airflow distribution can be balanced, and the pipe can be reduced. Vibration and ensure safe operation of equipment and piping. According to the production process, it can be divided into: welding elbows, punching elbows, casting elbows, etc.
Thick-walled elbows use high-quality wear-resistant steel as the basic material and can be used in pipeline systems in a variety of situations. Such as abrasive wear, corrosion wear, erosion wear, impact wear, etc.
Wear is one of the main forms of damage to thick-walled elbows. Wear causes a large consumption of energy and raw materials. According to incomplete statistics, 1/3 to 1/2 of energy is consumed by friction and wear.
In recent decades, the development and application of low- and medium-alloy wear-resistant steels have developed rapidly. Because these steels have good wear resistance and toughness, the production process is relatively simple, the overall economy is reasonable, and they are suitable for many working conditions. , and is welcomed by users. This also makes thick-walled wear-resistant elbows more widely used and cheaper.
Things to note when producing thick-walled pipe elbows:
1. Thick-walled elbows are also considered by many to be high-pressure elbows or wear-resistant elbows. Thick-walled elbow manufacturers usually use the stamping process during production, and sometimes they have to undergo heat treatment. Thin-walled elbows Generally, push-made elbows are used, and large-diameter thick-walled elbows must also be cut from medium plates. However, try to avoid using butt-welded elbows, because some suitable welds may not meet the requirements, so the technical requirements for welders are higher.
2. Thick-walled elbow manufacturers must conduct relevant inspections before leaving the factory to ensure that there are no cracks inside the thick-walled elbow, which may not be visible from the outside. Ultrasonic or flaw detection can be used to detect the size of the cracks. , and then repair. As a manufacturer of thick-walled elbows, Husteel combines production technology with advanced equipment to shorten the production cycle while ensuring the quality of thick-walled elbows.
3. Thick-walled elbows must be maintained regularly during use to extend their service life. According to project needs, manufacturers can also manufacture thick-walled elbows of various angles and specifications. Now more and more people are turning to carbon steel Thick-walled elbows are used as wear-resistant elbows because of their low price.
Application areas of thick-walled elbows:
Thick-walled elbows are widely used in petroleum gas pipeline engineering, natural gas pipeline engineering, chemical plants, power plants, shipyards, pharmaceuticals, dairy products, beer, beverages, water conservancy and other fields. These application fields cover many aspects of industrial production, including energy, chemical industry, food processing, etc., showing the important role and wide application of thick-walled elbows in various industrial environments.
Specifically, the application of thick-walled elbows in petroleum gas pipelines and natural gas pipeline projects ensures the safety and efficiency of energy transmission; in chemical plants and power plants, thick-walled elbows can withstand high temperatures and high pressures. environment, to ensure the smooth progress of the production process; in the shipbuilding, pharmaceutical, dairy, beer and beverage industries, thick-walled elbows ensure product quality and production safety. The selection of these application areas reflects the popularity of thick-walled elbows for their excellent performance and reliability.
Read more: Uses, types and standards of pipe fittings or Types of elbow fittings in piping
Related information