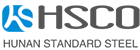
High frequency welding (HFW) is a new type of welding process that uses the skin effect and neighboring effect produced by high-frequency current to connect steel plates and other metal materials. The emergence and maturity of high-frequency welding technology is a key process in the production of ERW steel pipe. The quality of high-frequency welding directly affects the overall strength, quality level and production speed of welded pipe products.
Basic principle of high frequency welding:
The so-called high frequency refers to the frequency of the alternating current of 50Hz, and generally refers to the high frequency current of 50KHz to 400KHz. When high-frequency current passes through a metal conductor, two peculiar effects are produced: skin effect and proximity effect. High-frequency welding uses these two effects to weld steel pipes. So, what are these two effects?
The skin effect means that when an alternating current of a certain frequency passes through the same conductor, the current density is not uniformly distributed across all sections of the conductor. It will mainly concentrate on the surface of the conductor, that is, the density of the current on the surface of the conductor is high. The density inside the conductor is small, so we vividly call it: "skin effect". The skin effect is usually measured by the penetration depth of the current. The smaller the penetration depth, the more significant the skin effect. This penetration depth is proportional to the square root of the resistivity of the conductor, and inversely proportional to the square root of frequency and permeability. In layman's terms, the higher the frequency, the more current is concentrated on the surface of the steel plate; the lower the frequency, the more scattered the surface current is. It must be noted that although steel is a conductor, its magnetic permeability will decrease as the temperature rises. That is to say, when the temperature of the steel plate increases, the magnetic permeability will decrease and the skin effect will decrease.
The proximity effect refers to the fact that when high-frequency current flows in opposite directions between two adjacent conductors, the current will flow intensively to the edges of the two conductors. Even if the two conductors have another shorter side, the current does not follow. Shorter route flow, we call this effect: "proximity effect".
The proximity effect is essentially due to the role of inductive reactance, which plays a leading role in high-frequency currents. The proximity effect increases as the frequency increases and the distance between adjacent conductors becomes closer. If a magnetic core is added around the adjacent conductor, the high-frequency current will be more concentrated on the surface of the workpiece.
These two effects are the basis for realizing high-frequency metal welding. High-frequency welding uses the skin effect to concentrate the energy of the high-frequency current on the surface of the workpiece; and uses the proximity effect to control the location and range of the high-frequency current flow path. The speed of the current is very fast. It can heat and melt the edges of adjacent steel plates in a short period of time, and realize butt joints through extrusion.
Welding process:
Forming stage: The steel strip is gradually rolled into a tube through multiple rollers, and a V-shaped opening is formed on the edge (the opening angle is usually 2°~6°).
Heating stage: High-frequency current is introduced into the edge of the tube through a contact electrode or an induction coil, and the skin effect and proximity effect are used to melt the edge instantly.
Extrusion stage: Under the action of the pressure roller, the molten metal is squeezed and combined, and oxides and impurities are discharged to form a dense weld.
Cooling and shaping: After welding, the weld structure is quickly solidified by water cooling or air cooling, forming a joint with properties close to the parent material.
Key technologies for weld quality control:
(1) Process parameter optimization
Frequency selection:
Thin-walled tube (<6mm): 300~450kHz (heat concentration).
Thick-walled tube (≥6mm): 100~200kHz (deeper penetration).
Input power: adjusted according to the tube diameter and wall thickness (usually 50~1000kW).
Welding speed: usually 10~60 m/min, which needs to match the heating time.
(2) Defect prevention
Common defects: lack of fusion, pores, inclusions, cracks.
Control measures:
V-angle adjustment: Too small an angle can easily lead to lack of fusion, while too large an angle will increase energy consumption.
Extrusion pressure control: Insufficient pressure can easily leave residual oxides, while too large an angle can cause the weld to become thinner.
Protective gas: In some processes, inert gas (such as nitrogen) is injected to prevent oxidation.
(3) Post-weld treatment
Heat treatment: Normalizing or tempering can eliminate welding residual stress and improve weld toughness.
Weld grinding: Remove burrs on the outer surface to ensure the smoothness of the inner wall of the pipe.
Advantages and limitations of high-frequency welding:
(1) Advantages
High efficiency and energy saving: The welding speed is much faster than arc welding, and the energy consumption is low.
No filler material: The weld is pure and free of foreign impurities.
Strong adaptability: It can weld carbon steel, stainless steel, alloy steel, etc.
(2) Limitations
High equipment cost: High-frequency generators are expensive.
Wall thickness limit: It is usually suitable for pipes with a wall thickness of ≤20mm (thicker pipes require multiple passes of welding).
Material sensitivity: High carbon steel or high alloy steel requires strict temperature control to prevent cracks.
Application in ERW welded pipes:
Gas pipelines: High-frequency welded ERW pipes are certified by GB/T 9711, API 5L, etc. and are widely used in medium and low pressure natural gas transportation.
Structural engineering: Q235B/Q355B high-frequency welded pipes meet GB/T 13793 and are used in building steel structures, bridges, etc.
Conclusion:
High-frequency welding achieves efficient and high-quality connection of steel pipes by precisely controlling current, frequency and mechanical pressure. It is the core technology of ERW welded pipe production. The key to its success lies in the synergistic effect of skin effect and proximity effect, as well as the optimal matching of process parameters. Despite the problems of large equipment investment and limited thick-walled pipes, high-frequency welding is still an irreplaceable and cost-effective choice in the field of medium and thin-walled pipes (especially gas and structural pipes).
Read more: ERW pipe vs. HFW pipe or Types and uses of welded steel pipe
Related information