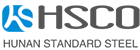
Concerns over the decline in oil resources are growing, and the temperatures and pressures in the wells and gas wells currently being mined are reaching unprecedented levels, with the liquids being mined generally containing carbon dioxide, resulting in more corrosion. Therefore, to prevent the flowline and collection pipeline from being corroded by carbon dioxide, it is extremely important to transport the liquid before removing corrosive substances and water. In addition, these liquids usually contain trace amounts of hydrogen sulfide, and therefore need to prevent chloride stress cracking. In this corrosive environment, for the carbon steel pipe material, the traditional anti-corrosion method is to inject liquid into the rust inhibitor, anti-rust agent to prevent corrosion. However, this increases the cost of production, especially offshore pipelines, so rust inhibitors are less commonly used, especially considering life cycle costs. Another reason not to use rust inhibitors is the fear of contamination from spills. Therefore, there is a need for an economical and economical material that does not require the use of a rust inhibitor. Existing pipeline corrosion-resistant alloys, including duplex stainless steel, but the disadvantage is the high cost of materials. In contrast, martensitic stainless steels generally have poor weldability and require preheating and longer post-weld heat treatment. Therefore, considering the pipe laying efficiency, martensitic stainless steel is rarely used in pipelines. However, martensitic stainless steels have adequate resistance to carbon dioxide corrosion and are cheaper than duplex stainless steels.
Related information