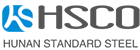
The complete ERW steel pipe production line mainly includes: decoiler-strip leveling-shearing butt welding machine-material cage / storage looper-forming machine-welding machine-burr removal-sizing machine-flaw detection-flying saw cutting -Initial inspection-steel pipe straightening-pipe section processing-hydraulic test-flaw detection and so on.
ERW steel pipe has the characteristics of relatively simple process and rapid continuous production, and is widely used in civil construction, petrochemical industry, light industry and other sectors.
It is mostly used to transport low-pressure fluid or manufacture various engineering components and light industrial products.
ERW steel pipe uses the principle of electromagnetic induction and the skin effect, proximity effect and eddy current heating effect of AC charges in the conductor to locally heat the steel at the edge of the weld to a molten state. The butt weld is extruded by rollers to achieve crystal indirection. In order to achieve the purpose of welding seam.
ERW steel pipe is a type of induction welded pipe. No weld filler is required, there is no welding spatter, the welding heat affected zone is narrow, the welding shape is beautiful, and the welding mechanical properties are good. Therefore, it is widely used in the production of steel pipes.
The related equipment of the erw steel pipe production line is mainly CNC cabinets, including: high-frequency main cabinet, high-frequency inverter cabinet, speed control cabinet (also commonly known as "drag"), computer flying saw CNC machine (also called "computer flying saw Console") etc.
Raw material characteristics:
·Pure steel, stable chemical composition, stable performance of steel grade;
·High precision of coil size, good shape control and good surface quality of coil.
Online detection technology:
·Ultrasonic board detection: detect layered defects and longitudinal long defects, and configure defect tracking paint spraying device to ensure 100% detection, tracking and removal of sheet defects.
·On-line weld ultrasonic flaw detection: Weld longitudinal and longitudinal defect detection, heat-affected layer detection and internal burr height control, mainly used for production process control.
·On-line flattening test: take samples for flattening tests at 0° and 90° of the weld and the pressure direction to ensure the basic performance requirements of the weld.
·Hydraulic test: Provide compactness guarantee for the base material and weld of each steel pipe.
·Off-line ultrasonic flaw detection of welds: magnetic particle flaw detection of pipe ends and groove surfaces, manual ultrasonic flaw detection of pipe ends and finished product size inspection.
Tips: ERW welded pipes are made by strip rolling and seam welding, with tighter dimensional tolerances and lighter weight. The weld is heat treated after welding so that no untempered martensite remains and the weld flash on the inner and outer surfaces can be removed. ASTM A53 ERW steel pipe is a typical carbon steel pipe. It is mainly used to transport low/medium pressure fluids such as oil, natural gas, steam, water, air and also in mechanical applications.
Related information