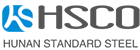
The corrosive media of sulfide corrosion are S, H2S, and SO, and the corrosiveness decreases in turn. The elemental S can penetrate the oxide film on the metal surface to reach the metal surface, react with the internal metal to undergo sulfidation, and cause the oxide film to crack and fall off. Similarly, when sulfur-containing fuels are burned in a reducing atmosphere, a large amount of HS gas will be produced. The HS gas diffuses and penetrates into Fe3O4, reacts with FeO or Fe therein, and generates FeS.
When the oxygen content in the combustion atmosphere increases, FeS will be further oxidized into S and FeO. At this time, FeO is sparse and porous and has no protective effect on the base metal, so the corrosion will continue. SO produced by combustion will react with HS gas to generate S, which will then become S corrosion. But in general, sulfide corrosion is mainly related to HS gas. S in high temperature environment rarely exists in the form of S.
At the same time, gaseous chloride will continue to be oxidized in a high concentration oxygen environment, regenerating metal oxides (FeO, FeO) and Cl. Compared with the original protective oxide film of the metal, it is looser, with poor density and adhesion, and loses its due protective effect, greatly reducing the transmission resistance of corrosive media such as HCl, Cl, O and SOx to the metal matrix interface, accelerating the corrosion of the metal matrix and the metal oxide film. Cl plays a self-catalytic role in this process, and very little Cl can maintain high-temperature gas phase corrosion. Molten salt corrosion refers to the reaction of the generated alkali metal sulfate with HCl to form the corresponding alkali metal chloride. In a high temperature environment, the alkali metal chloride exists in the gas phase and condenses on the colder metal surface to form corrosive deposits.
4. Reduction type high temperature corrosion
Reduction type high temperature corrosion occurs when there are incompletely burned gases such as CO, CH, H in the flue gas. When these reducing incompletely burned gases approach the heated surface, the iron-based oxide film and iron elements will be reduced to loose and porous ferrous oxide. When the oxygen content in the furnace is not less than 2%, the carbon monoxide content does not exceed 3% to 5%. When the oxygen content in the furnace of the boiler is relatively low, the carbon monoxide content will fluctuate greatly. Due to the chemical reaction of carbon monoxide and the iron oxide protective film on the water-cooled wall metal, the iron oxide protective film will react chemically, and then corrode the water-cooled wall. In general, the high-temperature corrosion process is very complicated, with mixed development of gas, liquid, and solid multiphase reactions, transfer in porous media, and interaction of the same and different terms, and is affected by multiple factors such as grain boundary processes, electrochemical processes, and stress evolution processes.
5. Ash accumulation corrosion
Ash accumulation refers to the deposition of fly ash particles in the flue gas with a temperature lower than the ash melting point on the heat exchange surface, which mainly occurs on the convection heat exchange surface. According to the ash accumulation strength, it can be divided into cohesive ash accumulation and loose ash accumulation: cohesive ash accumulation is generally formed on the windward side of the tube wall and grows along the airflow. The continuous growth of this ash accumulation will cause the resistance of the tube bundle to increase rapidly until the entire flue is blocked; loose ash accumulation is generally formed on the leeward side of the tube wall, and is formed on the flue gas surface of the tube wall when the particles are very fine or the flue gas velocity is low.
Taking the formation of ash accumulation during coal combustion as an example, the ash accumulation process of the heat exchange surface mainly includes fly ash formation, fly ash transportation, fly ash adhesion and growth. In the initial stage of ash accumulation, the temperature gradient between the ash layer and the flue gas is large, and the condensation of the volatile phase also has a significant effect on the initial stage of ash accumulation. Studies have shown that inertial collision is the main cause of ash accumulation. It is generally believed that large particles have greater inertia and can pass through the boundary layer and directly collide with the heat exchange surface; smaller particles mainly move to the heat exchange surface under the action of turbulence; for smaller particles, they mainly pass through the boundary layer under the action of Brownian motion and molecular diffusion to reach the heat exchange surface.
The influence of dust accumulation on corrosion is mainly manifested in the following two aspects: the stress damage effect of dense sintering dust accumulation and the diffusion corrosion reaction of chloride ions in the dust accumulation. Under high temperature conditions, the metal oxide layer on the heated surface produces cracks and defects under the stress impact of high-strength sintering dust accumulation. Some tiny dust accumulation particles slowly invade the cracks. The more mobile Cl− in the bottom dust accumulation diffuses into the metal oxide layer under the promotion of concentration gradient and temperature gradient, and reacts with the metal to form loose chlorides. In addition, the volatilization and outward diffusion of chlorides at high temperature cause the defects to be further aggravated, and the reaction continues. Ultimately, the combination of these factors leads to the shedding of the oxide layer. In the entire corrosion reaction, the diffusion process is the controlling step. This process is similar to the stress corrosion mechanism under the mechanochemical effect and the high-temperature cracking oxidation mechanism in corrosion theory. Both are caused by the combination of stress and corrosive environment to intensify corrosion.
In general, the formation of ash deposits is closely related to sulfate corrosion under high temperature conditions, molten salt corrosion in chlorine corrosion, and corrosion caused by the SNCR system. Molten corrosive salts will be produced on the high-temperature pipe wall, and a local liquid phase will be formed at the ash-metal interface, forming an electrochemical corrosion atmosphere, and the base metal will undergo anodic dissolution.
And as the wall temperature increases, the amount of molten material in the ash deposits outside the pipe wall will increase, resulting in an increase in the viscosity of the ash deposits, making it more difficult to be purged. The adhesion of ash deposits will cause the thermal conductivity of the pipe wall to deteriorate, and the pipe wall temperature will further increase. Excessive pipe wall temperature will further increase the number of corrosion products. The chemical reaction of NaCl, KSO, NaSO, etc. in the molten ash will cause the oxidative protective layer of the heated surface to be more seriously damaged.
High temperature anti-corrosion coating:
In order to prevent high temperature corrosion of boiler tubes, a relatively simple, economical, effective and convenient anti-corrosion coating method is usually used for protection. For example: high temperature resistant anti-corrosion coating, flue gas anti-corrosion coating, thermal conductive anti-corrosion coating, microwave absorbing heat-increasing coating, high temperature resistant ceramic radiation coating, etc.
Read more: Different types of boiler tubes and their role in energy or What are seamless boiler tubes and how are they made?
Related information