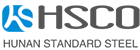
Hunan Standard Steel Co., Ltd is a professional manufacturer and supplier of seamless tube products such as oil and gas pipes, pressure vessel tubes (boiler tube), and mechanical tubes. Seamless steel tube products meet Chinese, American and European standards. We have advanced analytical instruments, online non-destructive testing facilities and a reliable quality assurance system to maximize the quality of products.
Manufacturing process of seamless tubes:
The production process of seamless tubes is a highly precise and complex process, which involves multiple key steps and quality control measures. Below, we will introduce the production process of seamless tubes in detail, including raw material preparation, perforation, rolling, heat treatment, finishing and inspection.
Rolling is the core link in the production of seamless tubes. During the rolling process, the rough tube is rolled and reduced through the rolling mill for many times, and the seamless tube of the required specifications is gradually formed. During the rolling process, parameters such as rolling temperature, rolling speed and rolling force need to be controlled to ensure the dimensional accuracy, wall thickness uniformity and surface quality of the steel pipe. In addition, the selection and configuration of the rolling mill are also important factors affecting the rolling quality.
The general rolling production process of seamless tubes can be divided into hot rolling and cold rolling (drawing):
1. Main production process of hot-rolled seamless tubes
Tube blank preparation and inspection-tube blank heating-piercing-rolling-steel pipe reheating-fixing (reducing) diameter-heat treatment-finished pipe straightening-finishing-inspection (non-destructive, physical and chemical, bench inspection)-warehousing.
2. Main production process of cold-rolled (drawn) seamless tubes
Blank preparation-pickling and lubrication-cold rolling (drawing)-heat treatment-straightening-finishing-inspection.
The production process of cold-rolled seamless tubes is generally more complicated than that of hot-rolled tubes. The pipe blanks must first be subjected to three-roll continuous rolling, and then to sizing tests after extrusion. If there are no cracks on the surface, the round pipes must be cut by a cutting machine into billets about one meter in length. Then they enter the annealing process, and the annealing must be pickled with an acidic liquid. During pickling, pay attention to whether there are a lot of bubbles on the surface. If there are a lot of bubbles, it means that the quality of the steel pipe does not meet the corresponding standards. In appearance, the cold-rolled seamless tube is shorter than the hot-rolled seamless tube. The wall thickness of the cold-rolled seamless tube is generally smaller than that of the hot-rolled seamless tube, but the surface looks brighter than the thick-walled seamless tube, the surface is not too rough, and the diameter does not have too many burrs.
Cold Drawing Process: Used to produce smaller seamless tubes from larger tube sizes.
Pilgering is one of the most widely used processes for producing seamless tubes ranging in size from ¼” to 2”, especially when the thickness of the tube needs to be reduced. Another process that can produce small seamless tube sizes is cold drawing.
Generally speaking, Pilgering has two main purposes:
First, and most importantly, Pilgering is a cold working process that can greatly improve the grain structure of the material.
Second, it is a method of very quickly reducing a large amount of the OD and ID of an existing tube. The reduction rate can be as high as nearly 90% for some alloys. The cold rolling process uses a ring die and a tapered mandrel to reduce the tube cross section by up to 90%.
The cold drawing process performs a similar job to the Pilgering process, but the size reduction rate is generally limited to 15% to 35%, depending on the alloy type.
6. Inspection
The production process of seamless tube is a highly sophisticated and complex process that requires the coordinated action of multiple links and quality control measures. By strictly controlling the quality of raw materials, optimizing the piercing and rolling processes, rationally selecting heat treatment methods and finishing processes, and strict inspection and control measures, high-quality seamless tubes can be produced to meet the needs of various industrial fields.
Read more: American Standard Seamless Steel Pipe or Seamless vs. Welded Tubing
Related information