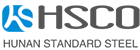
Manufacturing process issues: The manufacturing process of drill pipe has an important impact on its quality. Improper welding process, uneven heat treatment, etc. will cause changes in the internal structure of the drill pipe, which will affect its strength and toughness. These process problems will also cause drill pipe fracture during drilling.
Harsh use environment: During drilling, the drill pipe needs to withstand high temperature, high pressure and complex geological environment, which places high demands on the durability of the drill pipe. Especially in deep and ultra-deep well operations, the drill pipe is in a high stress state for a long time and is more likely to break.
2. Existing drill pipe quality inspection methods
In order to reduce drill pipe fracture accidents and ensure the safety of drilling operations, quality inspection is a key link. At present, the commonly used drill pipe quality inspection methods include:
Non-destructive testing: Non-destructive testing technology is widely used in the quality inspection of drill pipes, mainly including ultrasonic testing, magnetic particle testing and radiographic testing. These methods can effectively detect defects inside and on the surface of drill pipes, such as cracks, pores and inclusions.
Mechanical property testing: The mechanical properties of drill pipes are tested through tensile tests, impact tests and fatigue tests. Mechanical property tests can evaluate the strength, toughness and fatigue resistance of drill pipes, and provide a basis for the selection and use of drill pipes.
Chemical composition analysis: The chemical composition of drill pipe materials is tested through spectral analysis, chemical analysis and other methods to ensure that they meet relevant standards and requirements. The chemical composition of the material directly affects its mechanical properties and corrosion resistance.
Surface inspection: The quality and microstructure of the drill pipe surface are tested through microscopic inspection, metallographic analysis and other methods, and its surface defects and heat treatment effects are evaluated.
Corrosion test: Corrosion tests are carried out in simulated downhole environments to evaluate the corrosion resistance of drill pipes. Corrosion tests can help identify materials and parts prone to corrosion, so as to take corresponding protective measures.
3. The necessity of strengthening drill pipe quality inspection
In view of the frequent occurrence of drill pipe fracture accidents, it is particularly necessary to strengthen drill pipe quality inspection:
Improve drilling safety: Through strict quality inspection, potential defects and problems can be discovered and eliminated in time, and major safety accidents such as blowouts and well leakage caused by drill pipe fracture can be avoided, ensuring the safety of drilling operations.
Extend the service life of drill pipe: Scientific quality inspection can help identify the fatigue life and durability of drill pipe, reasonably arrange the use and maintenance of drill pipe, extend its service life, and reduce replacement costs.
Improve economic benefits: Drill pipe fracture will not only cause direct economic losses, such as shutdowns and equipment damage, but also cause huge indirect losses, such as project delays and waste of resources. By strengthening quality inspection, accidents can be significantly reduced, operating costs can be reduced, and economic benefits can be improved.
Promote technological progress: The development and application of quality inspection technology will help promote the advancement of drill pipe manufacturing processes and material technologies, improve the overall technical level of the industry, and enhance market competitiveness.
Suggestions and Prospects:
In order to effectively reduce drill pipe fracture accidents, the industry should take the following measures:
Improve standards and specifications: formulate and improve standards and specifications for drill pipe manufacturing, testing and use, clarify quality requirements and testing methods, and ensure that the quality of drill pipe meets relevant standards.
Strengthen technical training: provide professional technical training for drilling operators and testers to improve their operating skills and quality awareness, and ensure the correct use and maintenance of drill pipes.
Introduce advanced equipment: introduce and apply advanced testing equipment and technologies, such as high-precision ultrasonic detectors, portable magnetic particle flaw detectors, etc., to improve detection efficiency and accuracy.
Establish a monitoring system: establish an online monitoring system during drilling to monitor the working status and stress changes of drill pipes in real time, detect abnormal conditions in time, and take preventive measures.
Promote intelligent management: apply the Internet of Things, big data and artificial intelligence technologies to conduct intelligent management of the use and maintenance of drill pipes, optimize the use strategy of drill pipes through data analysis and prediction, and improve the management level.
Conclusion:
The frequent occurrence of drill pipe fracture accidents has brought serious safety and economic problems to the oil and gas industry. By strengthening quality inspection, the risk of accidents can be effectively reduced and the safety and efficiency of drilling operations can be ensured. In the future, with the continuous advancement of inspection technology and management methods, the quality and reliability of drill pipes will be further improved, providing a solid guarantee for the sustainable development of the oil and gas industry. All parties in the industry should work together to continuously promote technological innovation and management optimization to build a safer, more reliable and more efficient drilling operation system.
Go here to learn more: Difference between casing pipe and drill pipe
Related information