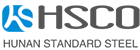
Seamless, by definition, means “perfectly consistent,” but many people get confused by terms like “seam-free” and “welded-and-drawn” when it comes to selecting tube. Seamless tubing, welded tubing, and seam-free tubing all appear to be consistently free of seams, but a closer examination reveals big differences.
Other industries using seamless tubes include the food processing industry (seamless stainless steel tubing), shipbuilding (seamless steel tubing)
How is Seamless Tubing Made?
Although preferable to welded tubes, seamless tubing requires a complex manufacturing process, which can significantly increase the price of the final product. Moreover, manufacturing long and wide seamless tubes can be challenging because they are directly related to the size of the billet and how advanced the manufacturing equipment is.
The manufacturing of seamless tubing starts by heating solid cylindrical or square-shaped billets to increase their malleability. Then, using a mandrel, the billet is pierced through the middle, creating a hollow tube. The tube is rolled to the desired thickness and length depending on the requirements.
Then, the tube goes through a series of dies to achieve a precise outer and inner diameter. This is followed by heat treatment in a vacuum furnace (air-drying is not recommended due to the danger of staining), which is crucial in giving the seamless tubing better mechanical properties, like increased strength and improved ductility.
The manufacturing process also involves straightening, as bends can be a weak point of seamless tubing. Finally, manufacturers use surface finishing, like cleaning, polishing, and applying a protective coating.
Quality control requirements for seamless tubing:
1. Material control: The quality of seamless tubes must first be controlled from raw materials, using high-quality raw materials, such as high-purity steel, to ensure the material performance and stability of seamless tubes.
2. Production process control: During the manufacturing process of seamless tubes, various parameters must be controlled, such as pipe making temperature, heater temperature, tube blank size, etc., to ensure that the diameter and thickness accuracy of seamless tubes meet the requirements while reducing defects.
3. Non-destructive testing: The testing of seamless tubes is an important means to ensure the quality of seamless tubes. During the manufacturing process, various non-destructive tests such as ultrasonic testing and magnetic particle testing are required to eliminate defects.
4. Mechanical property testing: The mechanical property testing of seamless tubes is also an important step in ensuring the quality of seamless tubes. The tensile strength, yield strength, elastic modulus, etc. of seamless tubes are tested to ensure the performance of seamless tubes.
5. Surface treatment: The surface treatment of seamless tubes also has a certain impact on its quality. Surface roughness, oxide scale removal, pickling and other processes are crucial to ensuring the quality of seamless tubes.
The significance of quality control of seamless tubing:
As an important steel product, seamless tubes are widely used in industrial production and civil fields. However, if quality control is not strict during the manufacturing process of seamless tubes, the following problems may occur:
1. Safety risks: Unqualified quality of seamless tubes may lead to the risk of accidents during production and use, resulting in personal and property losses.
2. Economic losses: Unqualified seamless tube quality will affect the service life and performance of seamless tubes, resulting in economic losses.
Therefore, it is very important to implement quality control of seamless tubes.
Read more: Carbon steel tube material and use or Seamless vs. Welded Tubing
Related information