What is a Thick-walled Seamless Steel Pipe?
Thick-walled Seamless Steel Pipes are made of high-quality carbon steel or alloy steel and are made through precision processes such as hot rolling, cold drawing or cold rolling. Their core feature is the integral structure without welds, which fundamentally eliminates the potential weak links caused by welds in traditional welded steel pipes. From the microstructure point of view, thick-walled seamless steel pipes have a dense arrangement of metal grains. This uniform organizational structure gives the material excellent mechanical properties and durability.
As an important basic material in the modern industrial field, thick-walled seamless steel pipes have an irreplaceable position in the energy, chemical, machinery manufacturing and other industries due to their excellent performance characteristics. This article will discuss the performance advantages of thick-walled seamless pipes (SMLS) from 9 aspects, including pressure bearing capacity, high temperature resistance, corrosion resistance, dimensional accuracy, processing performance, sealing performance, economic cost-effectiveness, environmental adaptability, and safety performance.
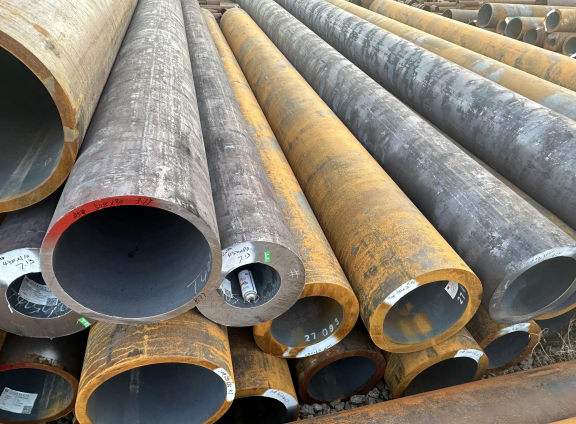
The performance characteristics and advantages of thick-walled seamless pipes are mainly the following:
1. In terms of pressure bearing capacity, thick-walled seamless steel pipes show significant advantages.
Thick-walled seamless pipes have high strength and durability. It is made of high-quality steel with excellent tensile and compressive strength. This allows it to withstand high loads and pressures while maintaining its shape and structural integrity. Taking the thick-walled seamless pipe made of #45 (1045 material) high-quality carbon structural steel as an example, its tensile strength can reach more than 600MPa and its yield strength exceeds 355MPa. This high-strength property enables it to withstand extreme internal pressure and external forces.
In the field of oil and gas transportation, this type of steel pipe can easily cope with working pressures exceeding 20MPa, ensuring the safety and stability of energy transportation. More importantly, due to the absence of welds, the pressure is more evenly distributed throughout the pipe body, avoiding stress concentration, which makes the service life of the pipe in a high-pressure environment more than 30% longer than that of
welded pipes. Thick-walled seamless steel pipes are very suitable for construction and engineering projects that bear huge weight and pressure.
2. High temperature resistance is another outstanding feature of thick-walled seamless steel pipes.
By adjusting the alloy composition, such as adding elements such as chromium and molybdenum,
thick-walled steel pipes can maintain stable mechanical properties in a high temperature environment of 600℃.
In the high-temperature and high-pressure steam pipeline system of thermal power plants, thick-walled seamless steel pipes can withstand a working temperature of 540°C for a long time without creep deformation. This heat resistance comes from two factors: first, the integrity of the seamless structure avoids the degradation of the weld under thermal cycles; second, the thick-wall design provides sufficient heat capacity, which slows down the impact of rapid temperature changes on the material. Experimental data show that seamless steel pipes of the same specifications are about 40% higher than welded pipes in thermal fatigue performance.
3. In terms of corrosion resistance, thick-walled seamless steel pipes can achieve multiple protections through material selection and surface treatment.
For acidic medium environments, corrosion-resistant alloy steels with copper, nickel and other elements are used; for oxidizing environments, stainless steel with a chromium content of more than 12% is selected.
In the application of chemical equipment, the uniform wall thickness distribution of large-diameter thick-walled seamless steel pipes ensures the consistency of corrosion rate and avoids the risk of local corrosion perforation. Surface treatment technologies such as galvanizing and plastic spraying further extend the service life of steel pipes in harsh environments. After testing, the corrosion resistance of thick-walled seamless steel pipes treated with hot-dip galvanizing in the marine atmosphere can reach more than 30 years.
4. Dimensional accuracy is an important indicator that distinguishes thick-walled seamless steel pipes from ordinary steel pipes.
The precision seamless steel pipes produced by advanced
cold drawing technology can have an outer diameter tolerance within ±0.05mm and a wall thickness deviation of no more than ±5%. This high-precision feature makes it the preferred material in the manufacture of precision mechanical parts such as hydraulic cylinders and bearing sleeves.
Taking the steel pipe for hydraulic support as an example, the inner surface roughness is required to reach Ra0.8μm or less, and only seamless steel pipes can meet such strict surface quality requirements. The direct benefit of precise dimensions is good interchangeability during assembly, which reduces the debugging time and operating failure rate of the mechanical system.
5. From the perspective of processing performance, thick-walled seamless steel pipes show good plasticity and machinability.
In the cold bending test, the high-quality
carbon steel seamless pipe can withstand 180-degree bending without cracking; in the expansion test, the pipe end can be expanded to 120% of the original diameter without breaking. This excellent formability enables the steel pipe to adapt to the processing needs of various complex shapes. At the same time, the hardness of the seamless steel pipe after normalizing is controlled below HRB90, which is very suitable for mechanical processing such as turning and drilling. In the manufacturing of automobile drive shafts, this characteristic enables the steel pipe to meet the strength requirements and facilitate subsequent finishing processes.
6. In terms of sealing performance, the overall structure of the thick-walled seamless steel pipe ensures absolute medium sealing.
In the application of the main steam pipeline of the nuclear power plant, the seamless structure completely eliminates the possibility of leakage of radioactive materials. Compared with welded pipes, seamless steel pipes will not have micro-leakage at the weld when subjected to pressure cycles. Test data shows that under the same working conditions, the air tightness of seamless steel pipes is two orders of magnitude higher than that of welded pipes, which is crucial for pipeline systems that transport toxic, harmful or expensive media.
7. From an economic perspective, although the initial purchase cost of thick-walled seamless steel pipes is higher than that of welded pipes, their full life cycle costs are more advantageous.
Taking the pipes used in petroleum cracking units as an example, the service life of seamless steel pipes is usually more than 15 years, which is 2-3 times that of welded pipes, and the frequency of maintenance and replacement is greatly reduced. In the energy industry, the losses caused by pipeline shutdowns and maintenance are often dozens of times the material cost, so the indirect economic benefits brought by the reliability of seamless steel pipes are more considerable.
8. In terms of environmental adaptability, thick-walled seamless steel pipes can meet various extreme environmental requirements by adjusting the material formula.
Seamless steel pipes used in Arctic oil and gas pipelines add nickel to improve low-temperature toughness and maintain good impact performance at -60°C; steel pipes used in tropical areas have enhanced resistance to wet and hot corrosion. This wide range of environmental adaptability makes seamless steel pipes a basic material choice for global industry.
9. From the perspective of safety performance, the failure mode of thick-walled seamless steel pipes is more controllable.
Since there is no weak link such as welds, steel pipes usually show uniform deformation rather than sudden fracture under overload conditions, which provides valuable safety warning time for engineering systems. In fields with extremely high safety requirements such as nuclear power and aerospace, this predictable failure mode is one of the key factors in selecting seamless steel pipes.
Conclusion:
Thick-walled seamless steel pipes have become the core material of modern industrial equipment due to their high strength, excellent sealing, good processing performance and reliable safety performance brought by their overall structure. With the advancement of manufacturing technology, new alloy thick-walled seamless steel pipes are constantly emerging, and their performance characteristics are also developing towards higher strength, better corrosion resistance, and better environmental adaptability, continuously meeting the increasing material needs of various industrial fields. From deep-sea oil and gas extraction to supercritical generators, from large chemical equipment to precision machinery manufacturing, thick-walled seamless steel pipes are supporting the development of modern industry with their excellent performance characteristics.
Read more: Thin Wall Seamless Carbon Steel Pipe or Mechanical Tubing vs. Structural Tubing